Radically Honest Services
Here are a few of the many ways we’re helping residential and commercial customers in DFW and beyond.
Lifetime Warranty
Steel Pier
For this popular method, we interlock 12-inch steel pipes with a friction reduction plate and fill the pipes with cement to prevent the piers from
failing. Steel piers can be driven up to 75 feet into the ground five times deeper than concrete
cylinders. And because they can bear a higher
load than any other foundation repair method,
they re a permanent solution.
Learn More… Lifetime Warranty
Steel
transition pier
Struggling to choose between steel and concrete
pier systems? Get the best of both worlds. Steel
transition piers mix double-walled steel and
high-strength concrete to provide a strong,
stable foundation at a reasonable cost.
Compared to a concrete pressed piling or a
drilled pier, it reaches deeper into the ground,
resting on the bedrock or very dense strata for
greater stability.
Learn More… Lifetime Warranty
Helical pier
These steel shafts with round helix plates
screw into the ground as deep as a steel pier,
until they reach enough kips, or measurements
in force. With minimal ground disturbance and
vibrations as well as quick installation, helical
piers are ideal for tying back bowed walls,
lifting fragile structures, and working with
sandy soils. Not always suitable for clay soil in
North Texas.
Learn More… 10-Year Warranty
Drilled pier
Drilled piers are an ideal foundation repair
solution for lightweight structures when
vibrations from a hydraulic press could cause
damage. We reinforce these 12- to 18-inch piers
with rebar and a five-sack concrete mix. Because
they only reach down to 12 feet into the ground,
they re only ideal if their reached depth either
surpasses or equates to that of steel or concrete
piling.
Learn More… 5-Year Warranty
Mud jacking
Mud jacking is a quick and affordable solution for
evening your foundation and fix the floating slabs
in your driveway, road, or pool. A mixture of
screened topsoil and cement is injected beneath
the slab through a two-inch drilled hole, lifting
the slab from underneath. However, if the soil
expands or contracts after the repairs, the
structure will move.
Learn More… 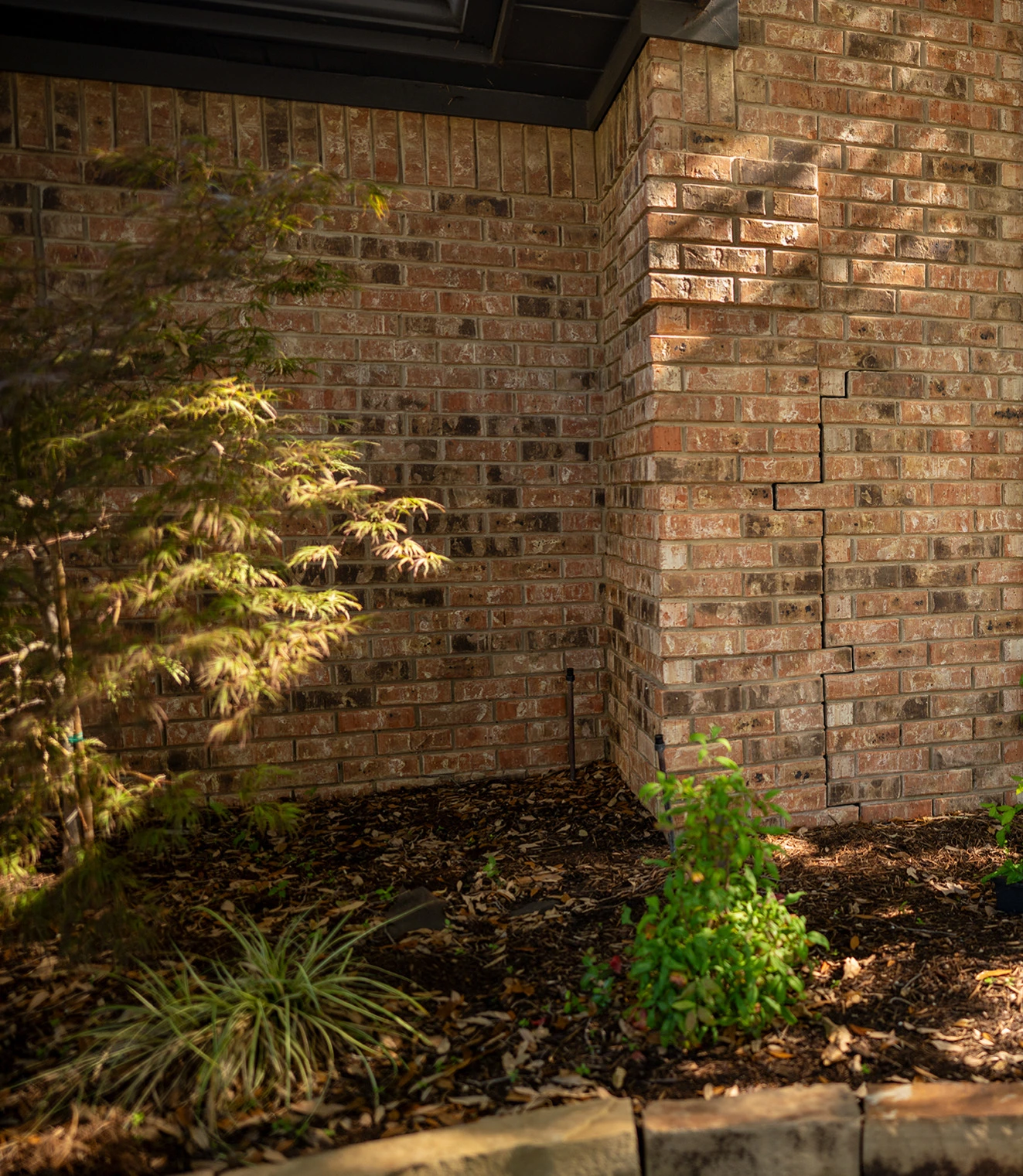
Radical Honesty means no guesswork or unpleasant surprises.
We use ground-penetrating radar to pull an exact image of your foundation instead of guessing how thick your foundation is or where interior grade beams may be located.
This ensures you:
Additional Services
2-Year Warranty
Pier and Beam/
Block and Base
Repair
If the floors in your house start sinking, you may have a pier and beam issue. Or, if your house is older, there may be a problem with your block and base foundation. We specialize in pier and beam as well as block and base foundation repair, and other services that go with it: wood replacement, pad and block systems, poured-in-place piers, and shimming existing piers.
Learn More… 5-Year Warranty
Drainage
Correction
Foundation problems aren’t always an expensive fix. If you have damage, you can prevent further issues by installing a proper drainage system. We specialize in installing surface drains with low-profile catch basins to trap incoming surface water, and deep French drains to remove subsurface water, preventing damp, mold, and foundation damage.
Learn More… Tunneling
For this method, we dig a tunnel to access your foundation from underneath your home if you don't want to damage expensive flooring or if it's impossible to vacate during the time of repairs. Although not cheap at first glance, if you consider other costs (replacing flooring after a slab breakthrough, moving furniture, hotel stay during time of repairs, etc.), it’s often worth it.
Learn More… 10-Year Warranty
Spread Footing
Spread footing creates a shallow foundation to support columns and walls, distributing the load from the structure to the soil beneath. We dig a 24x24x24-foot haunch below the existing structure, fill it with concrete, and reinforce it with rebar. Ideal for shallow rock areas or structures too light to hydraulically press a pier: retaining walls, wing walls, enclosed patios, or anything lacking a grade beam.
Learn More… 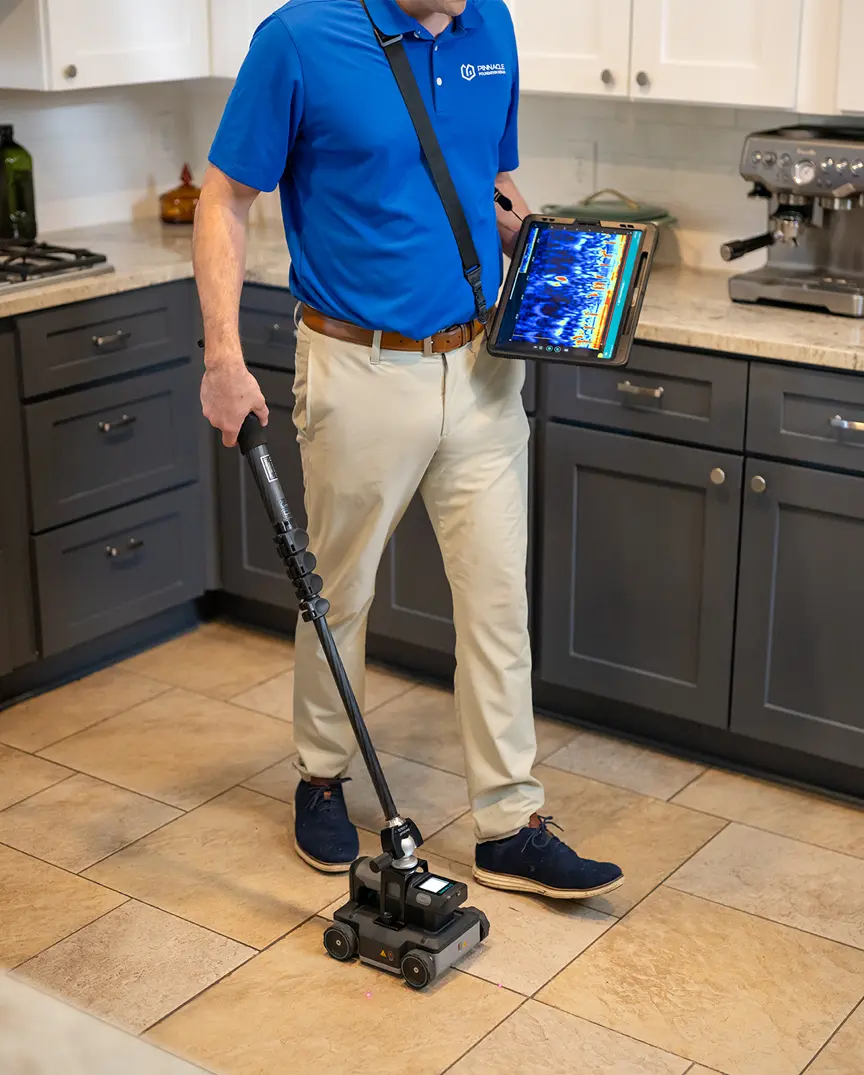
Schedule a FREE foundation evaluation
Don t wait till the cracks in the walls or the sticking doors become worse. Let us inspect your foundation free of charge, determine the cause of your problems and, if you have a foundation issue, give you a fair estimate. 1 out of 3 evaluations we conduct reveal no foundation issues
or call this number